پارامترهای کنترل کیفیت در سوراخ کاری: اطمینان از دقت و سازگاری
کیفیت سوراخهای تولید شده نقش بسزایی در عملکرد، ایمنی و قابلیت اطمینان محصول نهایی دارد.
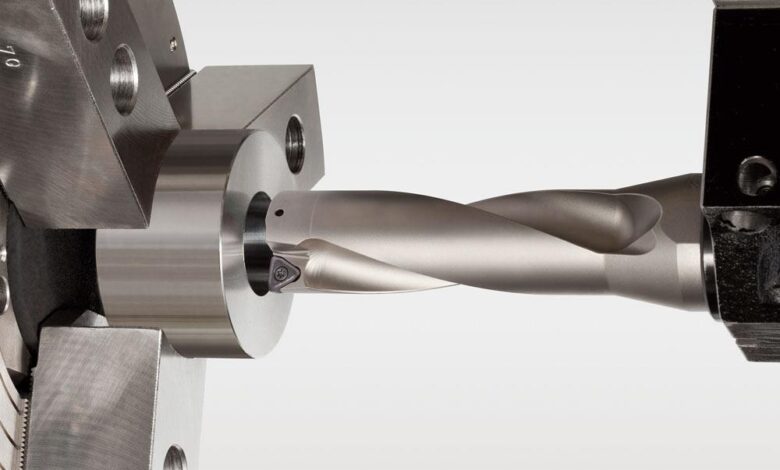
معرفی
سوراخکاری فرآیندی حیاتی در صنایع مختلف از جمله خودروسازی، هوافضا، ساختوساز و تولید است. این شامل ایجاد سوراخکاری و کنترل کیفیت در سوراخ کاری در موادی مانند فلزات، پلاستیکها و کامپوزیتها است. کیفیت سوراخهای تولید شده نقش بسزایی در عملکرد، ایمنی و قابلیت اطمینان محصول نهایی دارد. هدف این مقاله بررسی پارامترهای کنترل کیفیت ضروری است که باید در حین ایجاد سوراخ در نظر گرفته شود تا از دقت و سازگاری در محصول نهایی اطمینان حاصل شود.
انتخاب مواد و آماده سازی
اولین مرحله در ایجاد سوراخ، انتخاب ماده مناسب برای کاربرد و آماده سازی آن برای فرآیند است. خواص مکانیکی مواد مانند سختی، استحکام و شکل پذیری بر کیفیت سوراخ تاثیر میگذارد. آماده سازی مناسب مواد، از جمله تمیز کردن، چربی زدایی و عملیات سطحی، برای به حداقل رساندن بی نظمیهای سطح و اطمینان از ابعاد دقیق سوراخ، در کنترل کیفیت در سوراخ کاری حیاتی است.
روشهای حفاری و سوراخکاری
تکنیکهای مختلفی را میتوان برای ایجاد سوراخ استفاده کرد، از جمله مته زنی، قلاویز زنی و برقوکاری. هر تکنیک مزایا و محدودیتهای خود را دارد و انتخاب آن به مواد، اندازه سوراخ و دقت مورد نیاز بستگی دارد. طراحی، جنس و هندسه مته نیز بر کیفیت سوراخ تأثیر میگذارد. نگهداری و بازرسی منظم متهها برای اطمینان از اثربخشی و طول عمر آنها ضروری است.
ابزار و تجهیزات
کیفیت سوراخ به طور قابل توجهی به ابزار و تجهیزات مورد استفاده در طول فرآیند بستگی دارد. دستگاه مته، دستگاه فرز یا دستگاه CNC باید به خوبی نگهداری، کالیبره شده و مجهز به نگهدارنده ابزار مناسب و دستگاههای گیره باشد. استفاده از ابزار دقیق، مانند سیستمهای حفاری با کنترل کامپیوتر، میتواند دقت و ثبات را افزایش دهد و کنترل کیفیت در سوراخ کاری را ساده نماید.
نرخ پیشروی و سرعت برش
نرخ پیشروی و سرعت برش فاکتورهای حیاتی در ایجاد سوراخ هستند، زیرا میزان نفوذ مته به مواد را تعیین میکنند. نرخهای تغذیه بالاتر ممکن است منجر به تولید سریعتر شود، اما میتواند کیفیت حفره را به دلیل افزایش تولید گرما، ایجاد براده و سایش ابزار به خطر بیاندازد. از سوی دیگر، نرخهای پیشروی آهستهتر ممکن است. کیفیت سوراخ بهتری ایجاد کند. اما میتواند منجر به زمان تولید طولانیتر شود. نرخ تغذیه و سرعت بهینه باید بر اساس مواد، ابزار و کیفیت سوراخ مورد نظر تعیین شود.
خنک کننده و روانکاری
استفاده از مایع خنک کننده و روانکاری در حین ایجاد سوراخ برای به حداقل رساندن تولید گرما، کاهش اصطکاک و بهبود عمر ابزار ضروری است. خنک کننده همچنین به پاک کردن تراشهها و زبالهها کمک میکند و از تمیز بودن سوراخ اطمینان میدهد. انتخاب مایع خنک کننده یا روان کننده بستگی به ماده ای دارد که در حال پردازش است، زیرا برخی از مواد ممکن است به خنک کنندهها یا روان کنندههای خاص واکنش منفی نشان دهند.
دقت ابعادی سوراخ و دقت ابعادی
تلرانس سوراخ یکی از پارامترهای کنترل کیفیت در سوراخکاری است که به انحراف مجاز از اندازه سوراخ مشخص شده اشاره دارد. دستیابی به دقت ابعادی سوراخ مورد نظر به عوامل مختلفی از جمله خواص مواد، ابزار و پارامترهای فرآیند بستگی دارد. استفاده از ابزار دقیق و تجهیزات به خوبی کالیبره شده میتواند دقت ابعاد را به میزان قابل توجهی بهبود بخشد. بازرسی و اندازه گیری منظم سوراخهای تولید شده برای اطمینان از رعایت تلورانسهای مورد نیاز ضروری است.
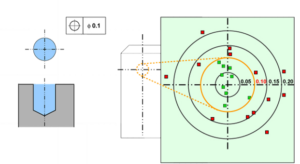
کیفیت سطح و ناهمواری سوراخ
پرداخت سطح و تشکیل سوراخ از پارامترهای کنترل کیفیت ضروری در سوراخکاری هستند. یک سطح خوب تمرکز استرس را به حداقل میرساند و ظاهر کلی محصول را بهبود میبخشد. از سوی دیگر، تشکیل سوراخ میتواند یکپارچگی سوراخ را به خطر بیندازد و ممکن است نیاز به عملیات تخلیه اضافی داشته باشد. انتخاب ابزار، پارامترهای برش و مایع خنک کننده میتواند بر روی سطح و شکل گیری سوراخ تاثیر بگذارد.
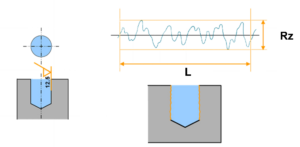
دقت هندسی و عمود
دقت هندسی و عمود بر هم ترازی و زاویه سوراخ نسبت به سطح قطعه کار اشاره دارد. تراز و زاویه مناسب برای یکپارچگی ساختاری سوراخ و عملکرد کلی محصول بسیار مهم است. اطمینان از اینکه دستگاه مته یا دستگاه CNC به خوبی کالیبره شده است و استفاده از ابزار دقیق میتواند به دستیابی به دقت هندسی و عمود بودن مطلوب کمک کند.
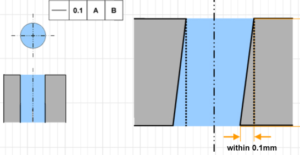
آزمایش غیر مخرب (NDT) و بازرسی
روشهای آزمایش و بازرسی غیر مخرب، مانند بازرسی بصری، اندازهگیری ابعاد و آزمایش اولتراسونیک، برای ارزیابی کیفیت سوراخهای تولید شده ضروری هستند. این روشها به شناسایی هر گونه عیب، مانند ترک، آخال یا انحراف از ابعاد مشخص شده کمک میکند. بازرسی و آزمایش منظم اطمینان حاصل میکند که سوراخها با استانداردهای کیفی مورد نیاز مطابقت دارند و برای هدف مورد نظر مناسب هستند.
بهبود مستمر و کنترل فرآیند
بهبود مستمر و کنترل کیفیت در سوراخ کاری فرآیند در حفظ و افزایش کیفیت فرآیندهای سوراخکاری بسیار مهم است. پیادهسازی یک سیستم مدیریت کیفیت قوی، مانند شش سیگما یا تولید ناب، میتواند به شناسایی زمینههای بهبود و بهینهسازی فرآیند حفرهسازی کمک کند. آموزش منظم کارکنان و توسعه مهارت نیز برای حفظ سطح بالایی از تخصص و مهارت در ایجاد سوراخ ضروری است.
نتیجه
پارامترهای کنترل کیفیت در سوراخکاری نقش بسزایی در اطمینان از دقت و ثبات محصول نهایی دارد. با در نظر گرفتن عواملی مانند انتخاب مواد، تکنیکهای حفاری، ابزارآلات، نرخ تغذیه و سرعت، خنککننده و روانکاری، تحمل سوراخ، پرداخت سطح، دقت هندسی، بازرسی و بهبود مستمر، تولیدکنندگان میتوانند سوراخهایی با کیفیت بالا تولید کنند که مشخصات مورد نیاز را برآورده میکند. به عملکرد کلی و قابلیت اطمینان محصول نهایی کمک میکند.