سوراخکاری چیست؟
از سوی دیگر، عملیات سوراخکاری درفلزات به فرآیند ایجاد سوراخ در قطعات فلزی با استفاده از ابزارهای تخصصی به نام مته اشاره دارد
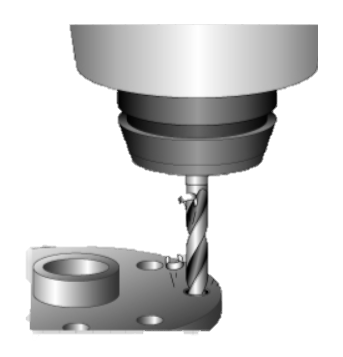
مقدمه
از سوی دیگر، عملیات سوراخکاری درفلزات به فرآیند ایجاد سوراخ در قطعات فلزی با استفاده از ابزارهای تخصصی به نام مته اشاره دارد. این عملیات در صنایع مختلف مانند خودروسازی، هوافضا، ساخت و ساز و مهندسی ضروری است، زیرا امکان ایجاد سوراخهای دقیق را برای اتصال دهندهها، پیچها یا سایر قطعاتی که نیاز به اتصال یا مونتاژ دارند، میسازد. در این مقاله، عملیات سوراخکاری در برش فلز، از جمله تاریخچه، انواع، اصول، تکنیکها، ابزار، مواد، اقدامات ایمنی و روندهای آتی را با جزئیات بررسی خواهیم کرد.
تاریخچه :
تاریخچه عملیات سوراخکاری فلز را میتوان به دوران باستان ردیابی کرد. جایی که از ابزارهای ابتدایی مانند مته های دستی ساخته شده از آهن، برنز یا سنگ برای ایجاد سوراخ در اشیاء فلزی برای اهداف تزئینی یا کاربردی استفاده میشد. این ابزار شامل یک مته متصل به یک دسته یا شفت بود. که به صورت دستی یا با کمک حیوانات یا نیروی آب میچرخید. متهها از مواد سختی مانند الماس، کاربید یا فولاد ساخته میشدند که میتوانستند دماها و فشارهای بالا را که در حین عملیات سوراخکاری ایجاد میشد، تحمل کنند.
انقلاب صنعتی پیشرفت های قابل توجهی را در فناوری سوراخ کاری به ارمغان آورد. زیرا ماشین آلات جایگزین کار دستی در صنایع مختلف از جمله فلزکاری شدند. اولین دستگاه سوراخ کاری به نام “ماشین فرز اوینورسال” توسط جوزف ویتورث در سال 1833 اختراع شد. که امکان تولید قطعات قابل تعویض با دقت بالا را فراهم کرد. این دستگاه از یک میز دوار، یک اسپیندل و یک مکانیسم تغذیه تشکیل شده بود که به مته اجازه میداد. به صورت عمودی و افقی حرکت کند تا سوراخ های دقیق ایجاد شود.
در اواخر قرن نوزدهم، اختراع موتور الکتریکی و توسعه مواد جدید مانند فولاد پرسرعت (HSS) و کاربید باعث ایجاد ماشینهای سوراخکاری قویتر و کارآمدتر شد. که میتوانستند مواد سختتر و ضخیمتر را با سرعتهای بالاتر سوراخ کاری کنند. و تغذیه میکند. معرفی طراحی به کمک کامپیوتر (CAD) و ساخت به کمک کامپیوتر (CAM) در اواخر قرن بیستم، انقلاب بیشتری را در عملیات سوراخکاری با ایجاد امکان ایجاد هندسه های پیچیده و پیچیده با دقت و تکرارپذیری بالا، متحول کرد.
انواع :
عملیات سوراخکاری در برش فلز را میتوان بر اساس هدف آنها به دو دسته اصلی طبقه بندی کرد:
سوراخ کاری خشن (که سوراخ کاری اولیه نیز نامیده میشود.) و سوراخ کاری نهایی (که به آن سوراخ کاری ثانویه نیز گفته میشود). سوراخ کاری خشن به عملیات اولیه سوراخ کاری اشاره دارد. که اندازه، شکل و محل تقریبی سوراخ را ایجاد میکند، در حالی که سوراخ کاری پایانی به عملیات سوراخکاری نهایی اشاره دارد که اندازه، شکل و محل دقیق سوراخ را در تلورانس های بسته ایجاد میکند.
سوراخ کاری خشن: عملیات سوراخکاری ناهموار برای ایجاد نقطه شروع برای عملیات سوراخکاری نهایی استفاده میشود، زیرا امکان حذف مقدار زیادی از مواد با یک بار عبور را فراهم میکند. و تعداد عملیات سوراخکاری مورد نیاز و هزینه و زمان کلی را کاهش میدهد. روند. عملیات سوراخکاری خشن همچنین برای ایجاد سوراخهای آزمایشی برای عملیات سوراخکاری نهایی استفاده میشود، زیرا آنها امکان تراز و موقعیت مته و کاهش نیروها و دماهای برش را فراهم میکنند.
سوراخ کاری نهایی: عملیات سوراخکاری نهایی برای ایجاد اندازه، شکل و محل دقیق سوراخ در محدودههای رواداری نزدیک به کار میرود، زیرا امکان حذف مقدار کمیاز مواد با عبور چندگانه، کاهش نیروها و دماهای برش و به حداقل رساندن خطر ابزار را فراهم میکند. سایش و شکستگی عملیات سوراخکاری پایانی همچنین برای ایجاد هندسه های پیچیده مانند کانتر سینک ها، پخ ها و مخروطی ها استفاده میشود، زیرا آنها امکان ایجاد زوایای، شعاع ها و اشکال خاصی را فراهم میکنند که تنها با عملیات سوراخکاری خشن به دست نمیآیند.
اصول عملیات :
عملیات سوراخکاری تحت چندین اصل است که نیروهای برش، دما و سایش و شکست ابزار را تعیین میکند. این اصول شامل موارد زیر است:
ناحیه تغییر شکل:
هنگامی که مته وارد قطعه فلزی میشود، یک ناحیه تغییر شکل در اطراف لبه برش ایجاد میکند که شامل تغییر شکل پلاستیک، تغییر شکل الاستیک و شکستگی است. تغییر شکل پلاستیک در مجاورت لبه برش رخ میدهد، جایی که قطعه فلزی توسط مته به کناری رانده میشود، در حالی که تغییر شکل الاستیک در قسمت بیرونی ناحیه تغییر شکل، جایی که قطعه فلزی تحت فشار و کشش نیروهای برش قرار میگیرد، رخ میدهد. . شکستگی در قسمت داخلی ناحیه تغییر شکل رخ میدهد، جایی که قطعه فلزی به دلیل نیروهای برش و درجه حرارت بالا به براده های کوچک شکسته میشود.
نیروهای برشی:
نیروهای برشی در عملیات سوراخکاری از تعامل بین مته و قطعه فلزی ایجاد میشوند. و از سه جزء اصلی تشکیل شدهاند: نیروی محوری (نیروی رانش نیز نامیده میشود)، نیروی شعاعی (نیروی تغذیه نیز نامیده میشود). و نیروی گشتاور (که به آن نیروی پیچشی نیز میگویند). نیروی محوری توسط عمل برش مته ایجاد میشود که تراشه های فلزی را از سوراخ بیرون میراند، در حالی که نیروی شعاعی از اصطکاک بین مته و قطعه فلزی ایجاد میشود که مته را به طرفین میکشد. نیروی گشتاور توسط عمل پیچشی مته ایجاد میشود که مته را حول محور خود میچرخاند.
دمای برش:
دمای برش در عملیات سوراخکاری در اثر اصطکاک و تغییر شکل بین مته و قطعه فلزی ایجاد میشود و در برخی موارد تا 1000 درجه سانتی گراد میرسد. که میتواند باعث اعوجاج حرارتی، سایش ابزار و شکستگی و همچنین مناطق متاثر از حرارت (HAZ) و تنش های پسماند در قطعه فلزی شود و میتواند بر خواص مکانیکی و عملکرد محصول نهایی تأثیر بگذارد.
سایش و شکست ابزار:
در عملیات سوراخکاری ناشی از نیروهای برشی، دما و مواد است و میتواند بر دقت، کارایی و ایمنی فرآیند تأثیر بگذارد. سایش ابزار را میتوان به دو دسته اصلی طبقه بندی کرد: فرسایش کناری و سایش دهانه. و سایش پهلوها در دو طرف مته اتفاق میافتد، جایی که نیروهای برش و دما بالا هستند. در حالی که سایش دهانه در نوک مته رخ میدهد. جایی که نیروهای برش و دما پایین است. شکستگی ابزار میتواند در اثر عوامل متعددی مانند بارگذاری بیش از حد، براده برداری، شکستگی و خستگی ایجاد شود و منجر به آسیب شدید مته، دستگاه و اپراتور و همچنین تولید محصولات معیوب و زیاد شود. هزینه و زیان برای شرکت و مشتری.
تکنیک های عملیات :
عملیات سوراخکاری در برش فلز به تکنیک ها و استراتژی های مختلفی برای اطمینان از دقت، کارایی و ایمنی فرآیند نیاز دارد، مانند:
انتخاب مته:
انتخاب مته برای موفقیت عملیات سوراخکاری بسیار مهم است. زیرا بر نیروهای برش، دما، سایش و شکستن ابزار و همچنین کیفیت و هزینه محصول نهایی تأثیر میگذارد. اندازه سوراخ، شکل، و محل، پرداخت سطح، عمر ابزار، و نرخ حذف مواد (MRR). انتخاب مته باید فاکتورهای زیر را در نظر بگیرد: خواص مواد مانند سختی، شکل پذیری و چقرمگی، ساختار دانه، عملیات حرارتی، و پرداخت سطح. پارامترهای سوراخ کاری، مانند سرعت، تغذیه، و عمق برش. شرایط سوراخ کاری، مانند مایع خنک کننده، روان کننده، و گیره؛ و اهداف سوراخ کاری، مانند بهره وری، دقت و قابلیت اطمینان.
هندسه مته:
هندسه مته عامل مهم دیگری است که بر عملیات سوراخکاری تأثیر میگذارد. زیرا نیروهای برش، دما، سایش و شکستگی ابزار و همچنین کیفیت و هزینه سوراخ را تعیین میکند. هندسه مته باید فاکتورهای زیر را در نظر بگیرد: زاویه مارپیچ، که سایش پهلو و تشکیل تراشه را تعیین میکند. زاویه آزاد، که نیروی شعاعی و عمر ابزار را تعیین میکند. و زاویه راس، که تعیین کننده نیروی برش و ضخامت تراشه است. زاویه پخ، که نقطه شروع و کنترل براده را تعیین میکند. و زاویه فلوت، که تخلیه تراشه و عمر ابزار را تعیین میکند.
پارامترهای سوراخ کاری:
پارامترهای سوراخ کاری مانند سرعت، تغذیه و عمق برش باید برای دستیابی به کیفیت و هزینه سوراخ مورد نظر بهینه شوند. و در عین حال نیروهای برش، دما و سایش و شکست ابزار را به حداقل برسانند. پارامترهای سوراخ کاری باید فاکتورهای زیر را در نظر بگیرند: خواص مواد مانند سختی، شکل پذیری و چقرمگی. هندسه مته، مانند زاویه مارپیچ، زاویه آزاد، و زاویه راس. شرایط سوراخ کاری، مانند مایع خنک کننده، روان کننده، و گیره بندی.
ماشینهای سوارخکاری:
مانند پرس سوراخکاری، مته دستی و ماشین سوراخکاری CNC باید بر اساس الزامات مانند خواص مواد، پارامترهای سوراخکاری و اهداف انتخاب و نگهداری شوند. ماشین های سوراخکاری همچنین باید به لوازم جانبی مختلفی مانند سیستم خنک کننده، سیستم روان کننده، سیستم گیره بندی و سیستم اندازه گیری مجهز شوند تا از دقت، کارایی و ایمنی عملیات اطمینان حاصل شود.
ایمنی :
ایمنی باید با رعایت اقدامات ایمنی مختلف، مانند استفاده از تجهیزات حفاظت فردی (PPE)، مانند عینک ایمنی، کفش ایمنی و دستکش ایمنی تضمین شود. استفاده از حفاظ های ماشینی مانند صفحه محافظ و نرده محافظ. استفاده از قفل های دستگاه مانند دکمه استارت/استاپ، دکمه توقف اضطراری و دکمه غیرفعال کردن دستگاه. و استفاده از تعمیر و نگهداری ماشین، مانند بازرسی منظم، روغن کاری، و تعمیر.
برای اطلاعات بیشتر با زیگ تولز در تماس باشید.